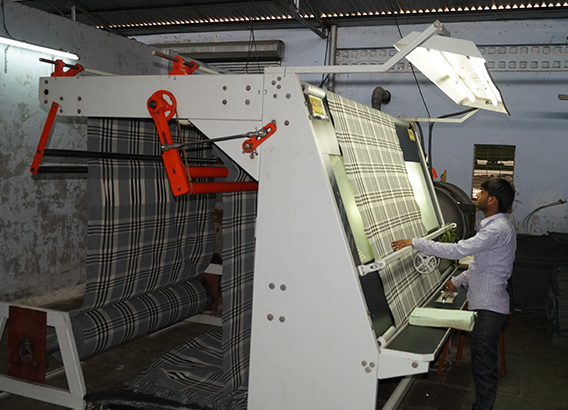
- Every 2 hours an independent QA inspector draws samples from the blend, card and spinning machine to check for composition, count, twist & strength to ensure that the floor level engineers findings are consistent with QA findings. This QA inspector is not reporting to the production team but rather directly to the management with their findings.
- During weaving every unprocessed roll is measured for length and weight in order to check for proper weights. Rolls are also randomly checked for compliance of construction parameters.
- Prior to processing each roll is visually inspected to see for any defects and such defects are either repaired if possible of marked to ensure that they do not get packed in your consignments.
- Post processing each roll is again visually inspected for any defects and such defects are either repaired if possible of marked to ensure that they do not get packed in your consignments.
- Records of all testing and checks are maintained in our records for a period of not less than 2 years to refer back to in case of any difference in findings between clients end and our end.
- Post finishing of the final blanket/throw each piece is again weighed and inspected whilst packing to make sure there are no defects. Only “Zero” defect goods are packed in your consignments.
- A proper preventive & breakdown maintenance schedule is followed to ensure that the machines are running properly and no inconsistency creeps into the product due to ill-maintained machines.